Customised product development
Intercarat partners with its customers in the production process, starting with design, development and the release of components and products. We place particular emphasis on what is called "Design for Manufacture" (DFM).
Co-engineering your moulded parts
We support your development department or your development service provider with our expertise in the area of elastomers, plastics, composite parts and the processing methods for them. For example, with regard to:
- Producibility
- Material and resource conservation
- Choice of materials
- Compounding of materials
- Compound development
- Analysis and test procedures
- Tool design/mould making.
You decide which services we provide to you, which subjects you want to develop, or whether other partners in your network should be commissioned with individual steps in development or design.
Costs and process reliability always in mind
Intercarat's technical office ensures that your products are designed so that they are appropriate for the material and can be manufactured on our machines without any problems. Our qualified employees check your product specification for possible undercuts and sharp edges, and if required change radii or parting lines and create demoulding aids. We also support you when it comes to reducing costs: We optimise wall thicknesses, moulds and tools and, if required, suggest changes to materials. You can provide us with your drawings and models directly in the file formats DXF, STEP and IGES.
High-quality precision parts made of rubber and plastic
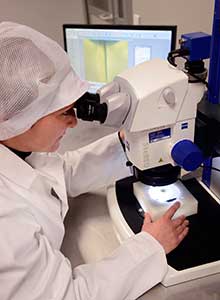
No-one likes to talk about "fault analyses". However, we believe that these are an integral part of each development cycle. Swell and ageing tests, Karl Fischer analysis or even rheology tests can provide important reference points, particularly for samples or pilot series, when striving to achieve a "perfect" moulded part for your product and its application. We can provide you with real-time information thanks to our state-of-the-art laboratory, making additional target-oriented modifications possible.
Intelligent choice of materials for practically all media and application conditions
Intercarat obtains materials and compounds exclusively from certified suppliers of raw materials and ensures that they comply with all legal standards. You can either state the material required, or we can find it for you. If you choose the latter option, please outline the physical and chemical parameters of the application as precisely as possible. This makes it possible for us to select the appropriate additives, such as carbon black (for reinforcement), and to order the compound. Furthermore, we can also manufacture test materials for initial samples especially for you on our mill in our manufacturing laboratory. We would be happy to find a cost-optimised solution for you.
Expertise in tool construction and mould making
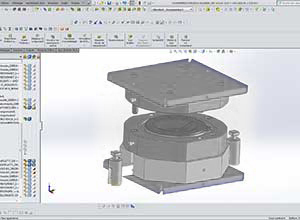
Intercarat will manufacture your tools and moulds for you. We have access to the full range of tool technology of the GEMÜ Group. Approximately 20 employees are in charge of the design and manufacture of injection moulding tools, elastomer injection and press tools, quench tools for PTFE/Teflon™ diaphragm manufacturing as well as clamping mechanisms and forming tools. Modern machinery with two 5-axis milling centres, a lathe with power milling/drilling tools, grinding machines and a networked production cell for hard machining with a 3D measuring machine are available to you. During assembly on the workbenches, the individual components are adjusted and combined with the standard parts to make a complete tool.
We can also rely on a network of established, long-term partners to supplement our own capacities. Collaboration with these design engineers also ensures the best possible expertise in the specific issues involved in plastic and elastomer processing as well as our manufacturing process, all of which contributes to the design and manufacture of the tools and moulds.